Elevate Quality Control with ibg NDT Technology: Precision, Safety, and Reliability for Your Industry Needs
In today's rapidly evolving industrial landscape, precision, safety, and reliability are paramount. At ibg NDT Technology, we understand the critical role that Non-Destructive Testing (NDT) plays in achieving these goals. With our state-of-the-art solutions, we empower industries worldwide to enhance their quality control processes and ensure the integrity of their products.
Decades of NDT Expertise: Leading the Way in Precision Technology for Aerospace, Automotive, and Manufacturing Industries
At ibg NDT Technology, we bring decades of expertise to the forefront of NDT technology. Our commitment to innovation and excellence has positioned us as trusted leaders in the field. Our NDT solutions are meticulously designed to meet the unique demands of industries such as aerospace, automotive, manufacturing, and beyond.
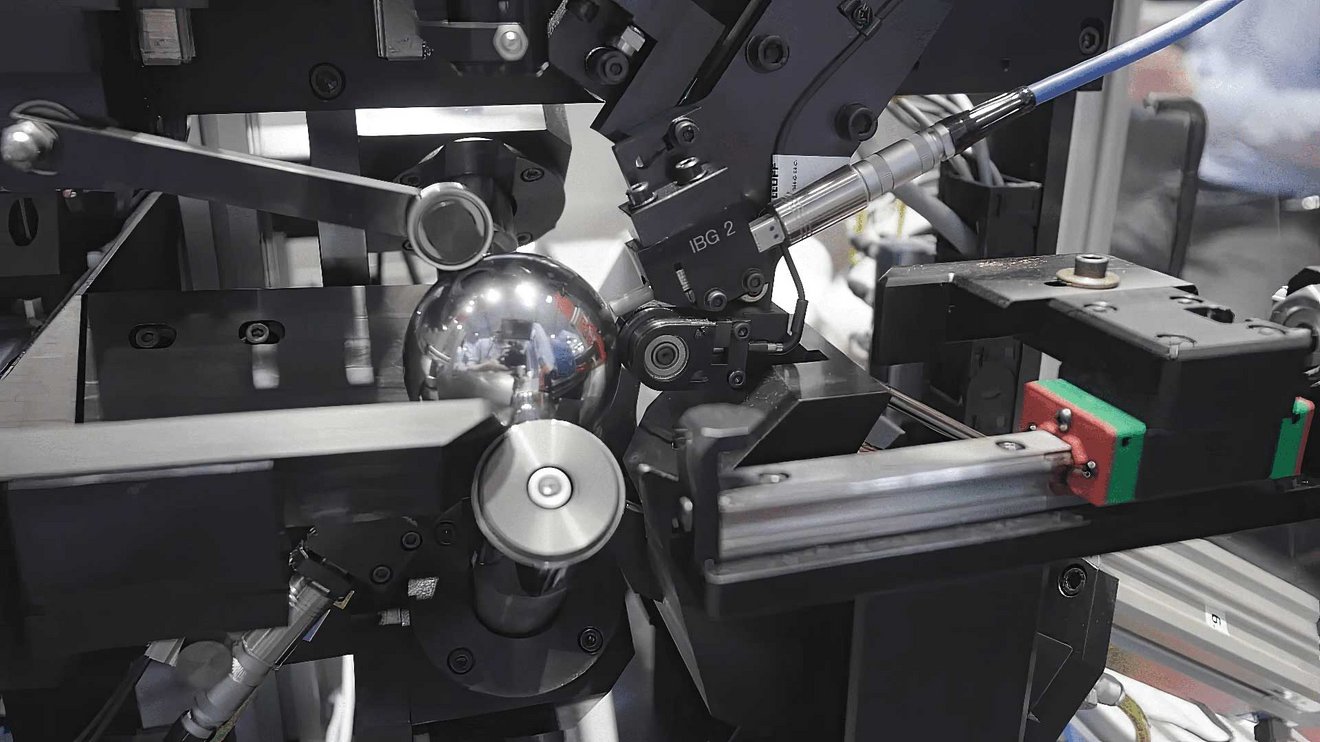
Precise and Reliable NDT Equipment: Ensuring Safety and Quality Across Industries
Our comprehensive range of NDT equipment encompasses a wide spectrum of testing methods, including eddy current, optical methods, and more. Each system is meticulously crafted to deliver precise and reliable results, ensuring the safety and quality of your products. Whether you're sorting components, detecting defects, or evaluating material integrity, our technology rises to the occasion.
Customized NDT Solutions for Every Industry: Seamless Integration for Precision Testing
We understand that no two industries are alike, which is why we offer customized NDT solutions to meet your specific needs. From aerospace components to automotive parts, our technology adapts seamlessly to diverse applications. Our team of experts collaborates closely with you to ensure that our NDT solutions integrate seamlessly into your production processes.
Your Trusted NDT Partner: Beyond Equipment – Comprehensive Support and Expertise
ibg NDT Technology doesn't just provide cutting-edge equipment; we offer a partnership. Our commitment to customer satisfaction extends beyond the sale, with comprehensive training, technical support, and maintenance services. We stand by your side, ensuring that you maximize the benefits of our NDT technology.
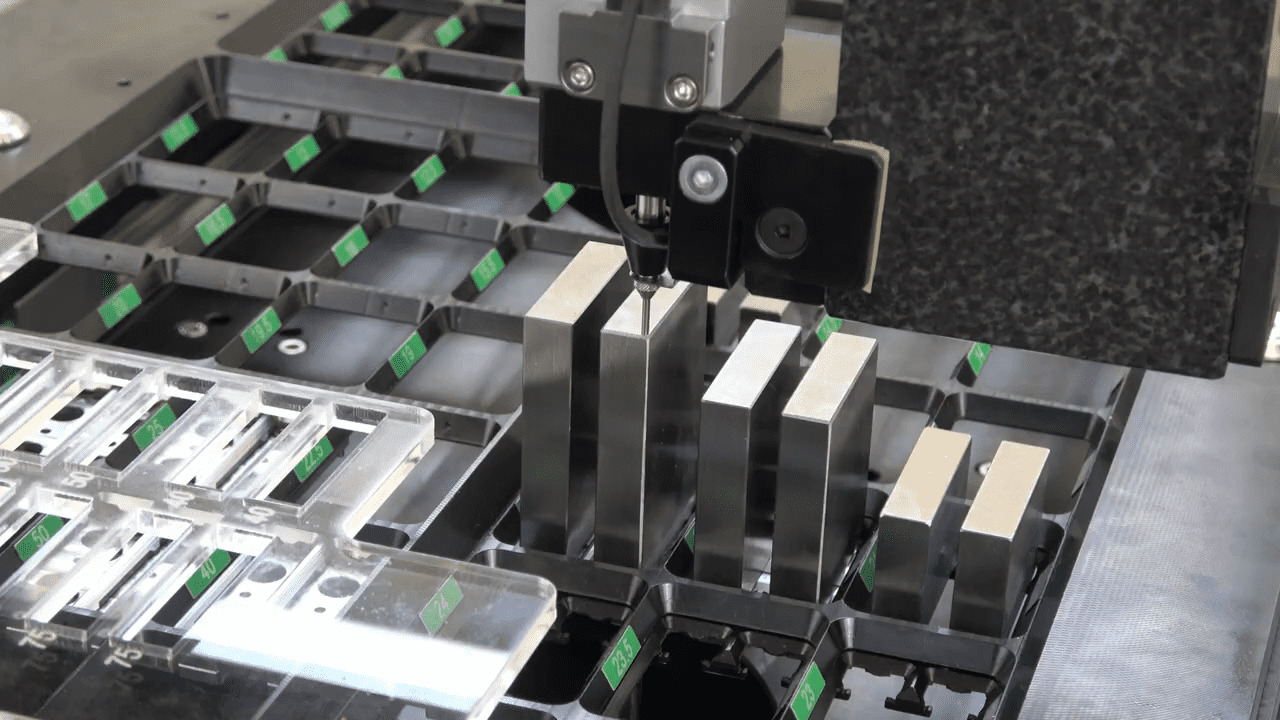
Staying Ahead of Industry Standards: ibg NDT's Commitment to NDT Advancements
As industry standards evolve, so do we. ibg NDT Technology remains at the forefront of NDT advancements, continuously refining our equipment to meet the latest requirements and regulations. Our dedication to innovation ensures that your quality assurance processes stay ahead of the curve.
Experience Unmatched Precision and Reliability with ibg NDT Technology
Join a growing number of industry leaders who rely on ibg NDT Technology to elevate their quality control processes. Our NDT technology isn't just about meeting standards; it's about exceeding them. Trust us to help you achieve unmatched precision, safety, and reliability in your operations. Contact ibg NDT Technology today and experience the future of non-destructive testing.
Contact Us